International trade offers businesses several growth opportunities but also exposes them to a variety of commercial, currency, documentary, and product risks. For instance, importers often face the risk of receiving inferior products, which adds to costs and causes reputational harm to exporters and manufacturers.
Pre-shipment inspection protects the interests of the manufacturer and importers as it ensures product compliance and maintains the desired quality standards. Further, it prevents product recalls and unexpected delays caused by non-compliant products.
Though the significance of pre-shipment inspection is known to most manufacturers, they make several mistakes that damage their reputation and customer trust. These mistakes could stem from product mishandling, weak packaging of goods, or poor environmental protection.
Businesses that fail to address these mistakes struggle with a serious product damage rate and dissatisfied customers. This post throws light on the common pre-shipment inspection mistakes that must be avoided at all costs.
But first, let’s dive into what pre-shipping inspection is and why it is important.
What Is Pre-Shipping Inspection?
Pre-shipping inspection encompasses processes followed by manufacturing and e-commerce businesses to meet the required quality standards and comply with international regulations before the product leaves the warehouse.
These inspections help in spotting defects and non-conformities before it’s too late. The pre-shipment inspector inspects products before 70-100% of the goods are packed for dispatch. They create a final report based on a pre-shipping inspection checklist (PSI).
What Pre-Shipping Inspection Does Not Include?
Pre-shipping inspection often seems like an umbrella term for the process followed before goods are shipped from a manufacturer or exporter to the buyer or importer. However, it is important to understand that it only involves inspecting the product from the buyer’s quality expectations point of view.
For instance, it covers aspects like:
- Quantity,
- Quality,
- Packaging,
- Labeling,
- and compliance-related matters.
So, the inspections are strictly for commercial cargo. It does not include /
- Warehousing,
- Freight forwarding,
- Or excess baggage checks, which are commonly included in passenger airline procedures.
To sum up, pre-shipping inspection is a part of the supply chain management process that focuses on quality control to ensure that the production quality complies with the set standards.
Significance of Pre-Shipping Inspection
Pre-shipping inspection ensures a smooth flow of goods and prevents several issues that could impact customer satisfaction and trust, and the business’s reputation.
Here’s why pre-shipping inspection is essential:
- It guarantees quality as per the legal guidelines and international standards in the destination country. The functionality, appearance, durability, and dimension check spots defects before shipping. It also ensures that the importer receives the right number of products. The inspection certificate holds all this information, allowing seamless passage of the goods through customs, thus improving the shipping process.
- It minimizes the risk for the seller and buyer. The importer receives goods as per their quality expectations, while the exporter can avoid additional costs and reputational damage.
- It facilitates the timely delivery of goods as issues are sorted before dispatch. This minimizes delays and fosters a strong relationship between the exporter and the importer.
- Allows businesses to focus on the specific needs of their buyers. With pre-shipping inspections, they can check the goods as per the unique requirements and ensure that they align with the criteria.
Now that you know about pre-shipping inspections, let’s move to the common mistakes businesses make in the process.
6 Common Mistakes to Avoid in Pre-Shipment Inspection
Let’s see what are the common mistakes and how to avoid them in order to complete a smooth and hassle-free pre-shippiment inspection.
1. Not Having a Pre-Shipping Inspection Checklist
A well-structured and detailed PSI checklist (pre-shipping inspection) is central to guiding the inspection team effectively. In the absence of this checklist, the inspector will not be able to establish the specific aspects that need inspection.
For instance, do they need to pay attention to the packaging and labelling requirements? Do they need to check the compliance documents relevant to the destination market?
Having clear documentation on the aspects to be inspected saves time and prevents misunderstandings during the inspection. It sets a roadmap for the inspection team on what needs to be done.
Here are a few points to be added to the checklist:
- Conduct sample testing using the AQL method at the initial stage
- Check the performance of electronic goods
- Classify defects by severity, especially for cosmetic and craftsmanship-based products
- Check dimensions for regulatory compliance
- Verify the total product count
- Verify packaging and labelling
Further, it is wise to have a pre-inspection check at your manufacturing site to avoid unpleasant surprises during the PSI. Conduct internal quality checks to identify and address issues before the formal check.
2. Failing to Have a Defined Inspection Criteria
Inspection teams focus on key areas like functionality, performance, durability, product and packaging dimensions, and overall appearance. However, a few products may require detailed inspection that needs to be clearly communicated to the inspection team.
For instance, electronics and industrial components need detailed inspection to ensure proper functioning and safety. Similarly, industry segments like pharmaceuticals or food products need specialized testing like composition analysis. Such requirements must be included in the inspection criteria.
The interpretation of regulatory standards for the inspector and other parties involved may differ, leading to disagreements and delays. Failing to define these specific standards and criteria for inspections can lead to back and forth and increase discrepancies in the process.
Further, in the absence of clear communication of expectations, the inspection team may miss critical elements and apply incorrect quality standards, leading to misleading inspection outcomes.
Establish a clear and detailed inspection criterion to ensure all the parties involved are aligned. Share a checklist, reference samples, and product manuals to keep them aligned with your expectations.
If the product being shipped needs extra tests, documentation, or certifications beyond the standard pre-shipping inspection, it should be mentioned to the inspection team.
For instance, goods being shipped to certain markets must comply with the ISO standards and REACH regulations.
DocShipper Alert
DocShipper Alert : Undefined or vague inspection criteria often lead to shipment rejections, customs issues, and unnecessary disputes between buyers and suppliers. Make sure your inspection scope is crystal clear, including reference samples and compliance standards. Don’t leave room for ambiguity, and consult DocShipper to help you build inspection protocols tailored to your industry!
3. Not Involving a Suitable Third-Party Inspection Company
Independent third-party inspection is critical to ensuring an unbiased inspection of the goods. It is a neutral third party that ensures that the goods adhere to the quality standards and the terms outlined in the purchase order.
It isn’t a good idea to rely on your internal manufacturing team to share this report, as it may be seen as biased and untrustworthy. Buyers are more likely to trust the findings of an independent inspection.
A third-party inspection report holds more value and builds trust with the buyer. These inspectors are trained and experienced to conduct inspections on a wide range of product categories. They provide a detailed inspection report with an overall pass or fail assessment and photos of defects. The report can be used as an official document to clear customs and manage disputes.
Select a suitable inspection service provider based on the factors shared below.
- Expertise: Look for service providers who have a proven track record and experience in the industry.
- Global Reach: The provider must have a strong presence and reputation for conducting inspections globally with teams present locally.
- Technological Capabilities: The company must be using advanced technology and tools to enhance the efficiency of the process and conduct accurate inspections. For instance, they must offer real-time data collection and analysis to facilitate immediate identification of issues and decision making.
- Open Communication: The inspection team must ensure clear and timely communication and proactively address issues for smooth operations.
DocShipper Alert
DocShipper Alert : Choosing the wrong inspection partner can threaten your shipment’s integrity. Third-party inspectors ensure objectivity and are often required by importers for customs clearance. Not sure which inspection partner fits your needs? Let DocShipper connect you with certified professionals globally. Contact us here.
4. Ignoring Packaging, Labelling, and Handling Instructions
Weak packaging and improper labelling put the goods at risk of being damaged in transit. For instance, adequate packaging and a label with ‘Fragile’ or ‘This side up’ guides carriers to handle the package accordingly.
Most businesses try to cut costs by compromising on the packaging. Yet, poor packaging costs businesses billions and is a key contributor to the losses incurred through returns and lost reputation.
Poor packaging and labelling lead to high return rates, delayed shipments, and additional costs. Here are a few points to consider when aiming for proper packaging and labelling:
- Opt for durable packaging materials, reinforced boxes, and high-quality cushioning to reduce the risk of breakage.
- Overstuffing can cause much damage. Ensure proper cushioning and spacing between products to prevent dents or other damage during transit.
- Shipping labels must carry adequate information on how the cargo is to be handled.
- Include clear barcodes and tracking details to prevent cargo misplacement.
Finally, don’t neglect the country-specific safety labels:
Here’s a list of prominent safety marks.
- UL Certification Mark (USA)
- The Canadian Standards Association mark, or CSA (Canada)
- The British Standards Institution mark, or BSI (UK)
- The CE mark (European Economic Area)
A few countries do not need pre-shipment inspections of goods. It is wise to check the local trading laws before shipping the products to those countries.
DocShipper Tip
DocShipper Advice : Do not underestimate the importance of packaging and labelling, it leads to costly product returns and transit damage. Custom packaging based on product type and destination regulations is essential. DocShipper helps you design compliant, durable, and cost-effective packaging solutions. Ask our experts to optimize your shipping process!
5.Ignoring the Documentation Involved
Not having the right documentation can result in delays and failed or inconclusive inspections. Make sure you have the necessary paperwork like compliance certificates, product specifications, testing protocols, invoices and purchase orders, and packing lists among other things.
Proper documentation aids smoother inspection, saving time, reducing costly delays, and helping the business stay compliant with regulations. Invest in a centralized document management system to organize critical trade documents, thus keeping them safe and easily accessible.
6. Not Staying Updated with the Regulatory Changes
Regulations governing imports and exports keep changing for each country. Staying on top of these changes in quality standards and regulatory requirements is critical to ensure compliance and avoid potential legal issues.
Failing to stay ahead of these changes can result in non-compliance and significant legal and financial consequences, like hefty fines, product recalls, and more.
Hence, it is important to consider the following pointers:
- Research the country-specific requirements and understand the pre-shipment inspection regulations of the countries you are exporting to.
- Partner with a reputed inspection company who have adequate knowledge and experience in the field.
- Ensure your team is well-versed in the legal aspects of pre-shipment inspections. Regular training and updates can help them understand the importance of compliance.
- Leverage technology like automated systems, software solutions, and digital inspection tools that can streamline the process of data collection, analysis, and reporting.
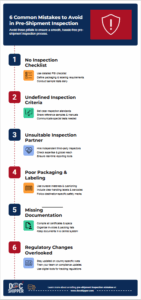
Conclusion
In today’s competitive trade scenario, ensuring quality and compliance is central to gaining a competitive advantage. Pre-shipment inspections (PSI) play a huge role in spotting defects before they leave the manufacturing facility, thus upholding the business’s reputation and improving the bottom line.
Pay attention to the common mistakes discussed in this post to streamline the pre-shipment inspection process. Proactively avoiding these mistakes can help you save costs and ensure product quality in global markets.
FAQ | 2025 Guide: 6 Mistakes to Avoid in Pre-Shipment Inspection
Read more
Looking for more? These articles might interest you:
DocShipper info: Do you like our article today? For your business interest, you may like the following useful articles :
Need Help with Logistics or Sourcing ?
First, we secure the right products from the right suppliers at the right price by managing the sourcing process from start to finish. Then, we simplify your shipping experience - from pickup to final delivery - ensuring any product, anywhere, is delivered at highly competitive prices.
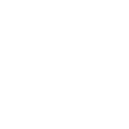

Fill the Form
Prefer email? Send us your inquiry, and we’ll get back to you as soon as possible.
Contact us